COLUMN

カーボンニュートラル実現に向けた3原則
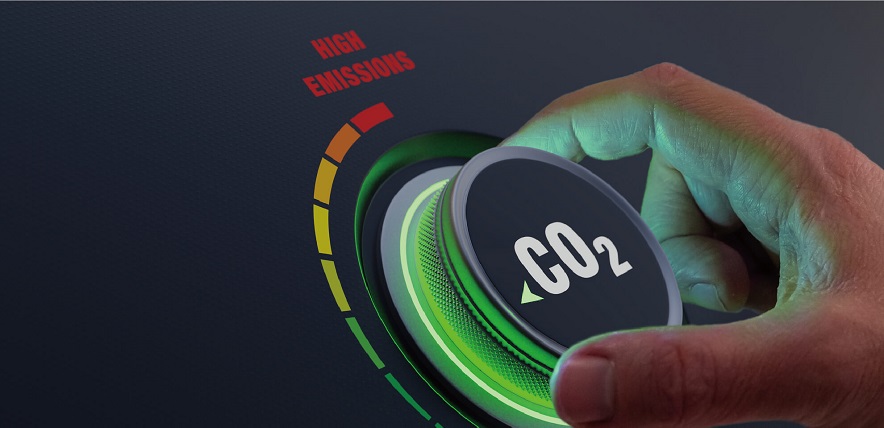
カーボンニュートラルを実現するための3原則は、①再生可能エネルギーへの移行②モノをつくる際に発生するCO2排出量の削減③技術革新によるCO2排出量の削減です。いずれも容易に実現できる課題ではないものの、だからこそ、多くの事業機会の誕生が期待されています。
昨今、「自動車業界は100年に一度の変革期を迎えている」といわれています。100年以上もの間、自動車の動力として絶対的なポジションにあったエンジンが「バッテリー」と「モーター」に置き換わりつつあること、電動化によって自動車の「コネクテッド化」が加速すること、「自動化」が進むこと、所有から利用へといった「シェアリング化」が進むことなどが、そのカギだとされています。
この変革によって、自動車業界の構造は大きく変わっていくことになります。ユーザーの立場で見ても、その変革は交通インフラだけでなく、生活を含めた社会のあり様そのものにまで及ぶ可能性があるのです。ではなぜ、自動車の電動化が必要なのか。そこを理解するためには、カーボンニュートラルに向けた世界的な動きや各国の規則、産業としての国策など、さまざまな国の思惑や動向を知る必要があるため、まずはカーボンニュートラルに関する基本的知識から触れていきたいと思います。
カーボンニュートラル目標
2020年10月、日本政府はアメリカやEU、イギリスなど他の先進国と足並みをそろえ、2050年までにCO2などの温室効果ガス排出を実質ゼロにするカーボンニュートラルを目指すことを宣言しました。そのための中間目標として2030年度に、「温室効果ガス排出量を2013年度から46%削減、さらに50%の高みに向けて挑戦を続ける」という野心的な目標を打ち出しています。
この宣言が世間に与えたインパクトは非常に大きなものがありました。上図から読み取れるように、翌21年から「カーボンニュートラル」に対する関心が急激に高まり、もっとも注目を集めるキーワードの1つになっています。この風潮は企業活動からも知ることができます。カーボンニュートラル実現に向けた事業変革に取り組み始める動きが活発化してきたからです。 ただ、カーボンニュートラル実現への道は容易ではありません。日本において、1990年以降でもっとも温室効果ガス総排出量が多かったのは2013年度で14億9000万トンですが、7年後の2020年度の総排出量は11億5000万トン(2022年速報値)と18.4%しか削減できていません。あと10年でさらに約3割も削減となる相当量の努力を必要とするのは間違いありません。
出典:資源エネルギー庁「国内外の再生可能エネルギーの現状と今年度の調達価格当算定委員会の論点案」(2022年10月)
カーボンニュートラル3原則
この高いハードルを越えるためには、次のような3原則ともいえるポイントがあります。
- 火力発電から再生可能エネルギーへの転換
- 製造プロセスにおけるエネルギー消費量とCO2排出量の削減
- 技術革新によるCO2排出量の削減
3原則いずれも容易に解決できる課題ではありませんが、だからこそ、その周辺領域で新たな技術やサービス、ソリューションが生まれ、新たな産業が立ち上がりつつあります。EVX(EVトランスフォーメーション)もその例外ではありません。この領域では、既にいくつもの事業が生まれ、あるいはその事業機会をとらえるための実証事業がさまざまな地域で実施されています。
火力発電から再生可能エネルギーへの転換
1つは、化石燃料による火力発電から再生可能エネルギーへの転換です。上図にあるように、日本のベース電源は天然ガスや石油、石炭などの化石燃料を使った火力発電であり、2050年にカーボンニュートラルを実現するためには、この割合を最低でも5~6割程度にまで高めていかなければならないといわれています。
しかし、日本は狭い国土に1億2000万人以上の人が暮らしています。しかも、国土の多くを山間部が占めていて平野に人が集中しているため、広大な敷地を確保して太陽光発電設備を設置するのが難しいという課題があります。そのため、今後はより一層住宅やオフィスビル、商業ビルといった建築物への太陽光発電設備の設置を促進していかなければならないでしょう。発電効率を飛躍的に高める技術革新も欠かせなくなってきます。
それなら風力発電を拡大すればいいと思うかもしれませんが、こちらも大きな課題を抱えています。ヨーロッパなどで主流となっている「着床式(海底に基礎を設置する形式)」の設置に適した遠浅の海域が少ないため、海に浮かべた構造物に設置する「浮体式」が主流にならざるを得ないからです。ところが、現状、浮体式は着床式よりも建設コストが1.5~2倍ほどかかるといわれており、収益化するのは簡単ではありません。また、浮体式の場合、養生設備から海底ケーブルを引いて発電した電力を運ぶ必要がありますが、このケーブル設置にも多額のコストが必要なうえ、環境汚染や環境破壊につながる恐れがあるため、地域の理解を得にくいといった問題もあります。洋上風力で発電した電力を巨大な蓄電池にためて電気運搬船で電力の消費地へ運ぶプロジェクトも動き出していますが、事業化されるのは何年も先だといわれているのが現状です。
出典:全国地球温暖化防止活動推進センター「日本の部門別二酸化炭素排出量の割合」(2020年度)
製造プロセスにおけるエネルギー消費量とCO2排出量の削減
2つ目のポイントはモノをつくるときに発生するCO2を減らすことです。CO2排出量というと、私たちの生活に身近な分、乗用車やトラック、バスなどの輸送部門がぱっと思いつくかもしれませんが、じつは全体の2割以上を占めているのは、輸送部門ではなく産業部門です。さらに、その内訳を詳しく考えてみると、9割以上が製造業によって占められており、中でも、鉄鋼、化学産業、セメントに代表される素材系製造業はエネルギー多消費産業といわれています。製造プロセスにおけるエネルギー消費量とCO2排出量を、いかに削減するかが大きな課題となっています。
例えば、日本では製鉄する際、鉄鉱石やコークス(石炭)を高炉と呼ばれる炉に投入して、炉の中で鉄鉱石から鉄だけを取り出すととともに、鉄鉱石を溶かす工程を一貫で行う「高炉法」という製鉄方法が広く採用されています。この方法ではコークスを大量に使うため多くのCO2が発生してしまうのです。こういった製造プロセスにおけるCO2削減を実現する方法の1つは、化石燃料で動いている機械などの電化を進めたり、発生したCO2を回収して再利用したり、貯蔵したりすることです。
ただし、電化を進めれば、当然、電力使用量は増加します。その電力を化石燃料による発電で賄うようなことになると、CO2排出量は減らせません。そのため、製造プロセスの電化を進めるのと並行してベース電源の再エネ化も推進していく必要があります。工場が太陽光設備を導入して自家発電に積極的に取り組んでいるには、こういった背景もあります。
技術革新によるCO2排出量の削減
また、中にはどうしても電化できない製造プロセスがあるでしょう。製鉄もその1つでしたが、近年はコークスの代わりに水素を使う「水素還元製鉄」という新しい技術の開発が進んでいます。水素は酸素と結びついて水になるため、理論上、CO2が発生せず、CO2削減につながるという技術です。これは世界的にもまだ実用化されていませんが、日本では世界に先駆けて、その目途がつきつつあります。
資料ダウンロードリンク
- UPDATE
- 2023.06.01